Продуманная, четкая организация работы склада — основное условие для выполнения складских операций с необходимой скоростью и высокой точностью. Именно на оптимизацию работы склада и направлено технологическое проектирование, результаты которого позволят рационально использовать имеющиеся площади, формализовать складские процессы, определить численность необходимого персонала и количество нужной техники и обстоятельным образом подготовиться к проекту автоматизации.
Потребность в технологическом проектировании может возникнуть в разных ситуациях: при строительстве нового склада, при переезде склада на новое место, при необходимости оптимизации процессов на уже работающем складе (в случае увеличения грузооборота, изменения параметров заказов, возникновении проблем, отражающихся на качестве обслуживания клиентов). Обращение к технологическому проектированию в одной из перечисленных ситуаций свидетельствует о том, что руководство предприятия осознает: рациональная организация склада и оптимизация складских процессов необходима для решения текущих проблем и предотвращения их возникновения в будущем.
Технологическое проектирование может выполняться как собственными логистами предприятия, так и привлеченной извне командой специалистов. Обычно на весь проект, проходящий в нормальном режиме, уходит порядка 25 рабочих дней.
Непосредственно перед началом работ по технологическому проектированию следует собрать всю необходимую информацию, касающуюся текущего положения дел на складе. Нужно знать, каким образом производится хранение и грузопереработка товаров, как отражаются в КИС данные об интенсивности и объеме товаропотока, каковы размеры и характеристики складских помещений, что представляет собой стеллажное оборудование, погрузочная техника и персонал склада. Чем более полной и точной будет полученная информация, тем больше гарантий, что по результатам технологического проектирования будут решены основные проблемы склада, связанные с оптимизацией процессов. Собранная информация также сможет быть использована в проекте автоматизации склада, т.е. результат одной и той же работы определенно может быть использован дважды.
Сам технологический проект выполняется в несколько этапов. На первом этапе производится разработка наилучшего объемно-планировочного решения.
Каким должен быть склад?
Проанализировав данные о поставках и отгрузках в периоды пиковой активности склада, можно определить оптимальные размеры зон разгрузки, приемки, комплектации и отгрузки. Зная средний уровень запаса каждого наименования за период, в который наблюдались наибольшие остатки на складе, рассчитываем оптимальные типоразмеры и количество ячеек. По результатам расчетов принимается решение о том, необходима ли установка стеллажей, либо есть возможность ограничиться штабельным хранением. Высота хранения, количество рядов и ширина проездов между ними определяются параметрами помещения, характеристиками имеющегося (или запланированного к приобретению) стеллажного и подъемно-транспортного оборудования, а также требованиями пожарной безопасности.
На выходе получаем несколько вариантов планировок, отличающихся друг от друга по размеру финансовых вложений. Так, минимум инвестиций потребуется при организации штабельного хранения, но тогда речь может идти о снижении эффективности использования объема хранения (существуют ограничения по высоте штабелей); максимально эффективное использование вместимости склада возможно при постановке набивных стеллажей, однако во многих случаях они ограничивают доступ к части товара. Свободный доступ к любому товару обеспечивается при установке фронтальных стеллажей, но в этой ситуации эффективно используется только 35–40% общей площади склада. В каждом конкретном случае приходится выбирать, какой именно фактор (размер инвестиций, эффективность использования площадей и вместимости, оперативность доступа к товару и т.п.) при планировке склада является для данного предприятия приоритетным.
Выбрав из предложенных вариантов оптимальный, следует переходить ко второму этапу технологического проектирования, на котором будут проработаны технологии грузопереработки, определено количество персонала, штатное расписание, график работ.
Как должны выполняться складские операции?
Складские процессы могут быть разделены на две основные группы: регулярные и периодические. К регулярным относятся операции, выполняемые ежедневно: разгрузка, приемка, размещение, отбор, упаковка, отгрузка и т.д. Периодические операции выполняются в случае возникновения нестандартных ситуаций. К таким операциям могут быть отнесены работа с браком, организация возврата поставщику, выборочная инвентаризация и т.п.
После создания перечня всех операций для каждой из них составляется подробная рабочая инструкция с описанием состава работ, исполнителей, информации, необходимой для ее выполнения, исходящих документов и используемых технических средств. Дополнительно следует разработать логику, согласно которой будут приниматься решения о том, как следует размещать принятый товар, когда производить подпитку активной зоны хранения, в какой последовательности производить отбор по заказам и т.д. Таким образом, будут подготовлены алгоритмы повседневной работы склада.
Какова потребность склада в персонале и технике?
Еще при разработке алгоритмов выполнения складских операций, указывая исполнителей, рекомендуется максимально детализировать их функции, что позволит точнее определить потребность склада в персонале. Число необходимых сотрудников зависит и от объемов товарных потоков, и от времени, необходимого для выполнения каждой операции.
Существует несколько формул, позволяющих рассчитать потребность склада в персонале, отталкиваясь от исходных данных. Ниже приведена одна из них.
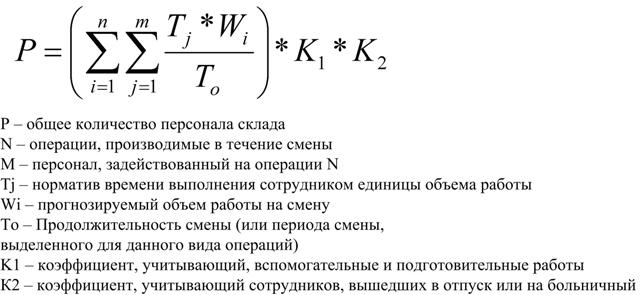
По указанной формуле для каждой операции в отдельности следует определить необходимое количество исполнителей. Во всех случаях полученный результат необходимо скорректировать, используя коэффициент неучтенных работ, в который закладываются вынужденные простои, время ожидания и т.д., что увеличивает время выполнения работ в 1,2 — 1,35 раза.
Далее принимается решение о том, исполнителем какого количества операций может выступать один складской работник, в соответствии с его опытом, знаниями и квалификацией. Определив число сотрудников каждой специализации в одной рабочей смене, умножаем полученное значение на число смен, учитываем такие явления как отпуск и уход на больничный и в итоге получаем окончательное штатное расписание с фиксированным количеством персонала. Следующим шагом определяются функциональные обязанности и составляются должностные инструкции сотрудников.
Потребность склада в техническом оборудовании рассчитывается уже исходя из полученных данных о числе персонала. Заложив в математическую модель расчета потребности в персонале информацию о трудовых и технических ресурсах, можно получить данные о необходимом количестве каждого вида технических средств (погрузчики, штабелеры, лифты, стремянки, сканер штрих-кода и т.д.). Например, если при разгрузке транспортного средства участвуют 2 грузчика, кладовщик и водитель погрузчика, то, соответственно, грузчики пользуются гидравлическими тележками, а водитель погрузчика — погрузчиком. Количество человеко-часов на разгрузку определяется объемом грузопереработки за смену. Соответственно, можно определить период времени, в которое используется та или иная техника.
Технологический проект склада и автоматизация.
Итак, один из результатов технологического проектирования — документ, в котором максимально подробно описаны все расчеты, обоснован выбор определенного варианта объемно-планировочного решения, зафиксированы алгоритмы работы склада и должностные инструкции, подсчитана потребность склада в персонале и технике. После внесения в работу склада изменений, соответствующих результатам технологического проектирования, можно остановиться на достигнутом эффекте, но правильней двигаться дальше.
В подавляющем большинстве случаев технологический проект становится шагом, предшествующим автоматизации склада. Руководству предприятия, принявшему решение о внедрении системы управления складом (WMS), не следует забывать, что автоматизация, помимо релевантных исходных данных о товаре и топологии, требует четкого представления обо всех складских бизнес-процессах. Поэтому выполнение технологического проекта, оптимизирующего и упорядочивающего работу склада с учетом возможностей WMS, является идеальной подготовкой к внедрению. Конечно, существуют компании, склады которых и без специальных мероприятий уже работают четко и отлажено, где автоматизация преследует цель увеличения скорости операций и повышения их точности — в таких ситуациях новое технологическое проектирование не является жизненно необходимым.
С другой стороны, иногда за технологическим проектом может и не последовать автоматизация склада. В ряде случаев оптимизации площадей и бизнес-процессов, проведенной по результатам технологического проектирования, бывает достаточно для того, чтобы решить основные проблемы склада, и о внедрении WMS речь не идет изначально. Однако с ростом конкуренции, повышением требований контрагентов предприятия к грузообработке на складе таких случаев становится все меньше и меньше.
Технологический проект, впрочем, как и автоматизация склада, — не панацея от всех бед, но именно его разработка и внедрение способны действительно улучшить работу склада. Рациональное использование складских площадей, формализация всех процессов, оптимальные численность персонала и количество техники — эти результаты технологического проектирования являются обязательными условиями эффективной работы склада и залогом успешной автоматизации. По крайней мере, десятки выполненных AXELOTLogistics проектов это подтверждают.
Дарья Любовина, руководитель проектов AXELOT
Ольга Каверина, консультант по складской логистике AXELOT