С процессом комплектации связаны многие показатели эффективности работы склада, коммерческого отдела, процесса обслуживания клиентов в целом. Качество выполнения заказов создает определенный имидж компании на рынке и обеспечивает ей тот или иной уровень конкурентоспособности.
На работу склада в процессе выполнения заказов затрачивается наибольшее количество ресурсов. Поэтому чем точнее происходит планирование ресурсов, тем быстрее и качественнее склад выполняет свою работу по комплектации заказов клиентов.
В процессе выполнения заказов клиентов существует несколько этапов, в которых возможна оптимизация. Но прежде чем рассматривать методы оптимизации, разберем этапы самого процесса выполнения заказов.
Как правило, заказы клиентов принимают и обрабатывают сотрудники коммерческого отдела, передавая их далее на склад, где заказы трансформируются в задание на отбор товара и подготовку заказа к отгрузке. В процессе регистрации заказа менеджер по работе с клиентами пользуется информацией об остатках товара на складе, номенклатуре, партиях, сериях, сроках годности.
После регистрации заказа клиента в Корпоративной информационной системе (КИС) заказ поступает в Автоматизированную систему управления складом (АСУ склада). Оператор склада формирует задание на отбор товара, передает задание комплектовщикам.
Происходит отбор товара, передача его в зону контроля и упаковки. Затем скомплектованный и готовый к отправке клиентам заказ размещают в зоне отгрузки.
Согласно опыту реализации проектов AXELOT, существуют 4 основные области оптимизации рассматриваемого процесса (Рис.1):
1. Этап приема и обработки заказа
2. Обмен информацией между складом и коммерческим отделом
3. Планирование операции отбора и выдача задания комплектовщикам
4. Передача отобранного заказа в зону контроля. Проверка и упаковка товара
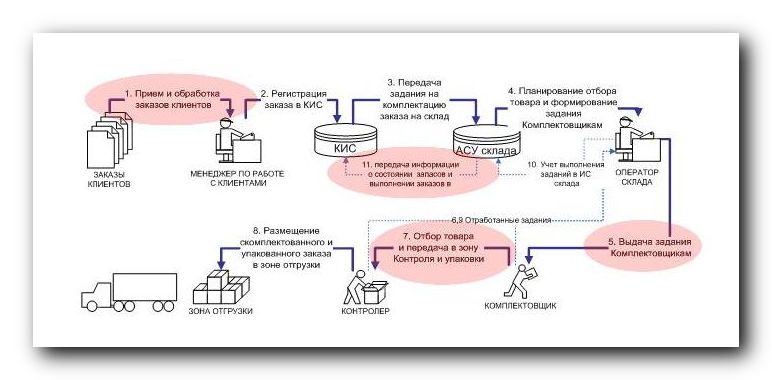
Прием и обработка заказов клиентов
Выделяются три фактора, которые могут повлиять на стабильность работы склада на этапе размещения заказа клиентом: срочность заказов, неравномерность поступления заказов и размещение дополнительных заказов одним клиентом на одну дату отгрузки.
Многим знакома ситуация, когда основная масса заказов приходит под вечер, а отгрузка товаров предполагается уже утром. При этом утром могут поступить срочные заказы, которые необходимо отобрать и упаковать до начала утренней отгрузки. Эта проблема, в первую очередь, актуальна для распределительных центров (поставщиков розничных магазинов), а также для складов готовой продукции пищевых производств. Для склада такая динамика оборачивается авральными работами, необходимостью организовывать ночную смену.
Нередко розничные магазины размещают несколько заказов в течение дня в зависимости от изменения текущего спроса на товары. Это, в свою очередь, увеличивает время на обработку заказов операторами, а также суммарное время на комплектацию заказов на складе. Немногие компании идут на то, чтобы установить четкий график размещения заказов, и проблема неравномерного поступления заказов, как правило, решается с помощью организации второй смены (во второй половине дня, либо ночной).
Размещение срочных заказов или множества дополнительных заказов можно снизить, разработав особую ценовую политику. Например, не предоставлять скидки на дополнительные и срочные заказы или ввести надбавочный коэффициент. Однако такой метод не ликвидирует проблему дополнительных заказов полностью. Поэтому прежде чем заказы будут переданы на склад для комплектации, рекомендуется их дополнительно обработать с целью объединения заказов на один адрес доставки (рис.2).
До тех пор пока заказы не переданы в качестве заданий на отбор товара, они накапливаются в базе КИС или АСУ склада, где возможна их автоматическая обработка.
Поступающие заказы от клиента с одинаковыми параметрами (клиент, адрес доставки, номер договора, категория заказа, дата отгрузки) должны быть объединены в один заказ. При этом вычисляется суммарное количество идентичных товаров. Проверка критериев должна производиться сразу после поступления очередного заказа в информационную систему. Это позволит сократить общее количество заказов, а значит, и время на их комплектацию.
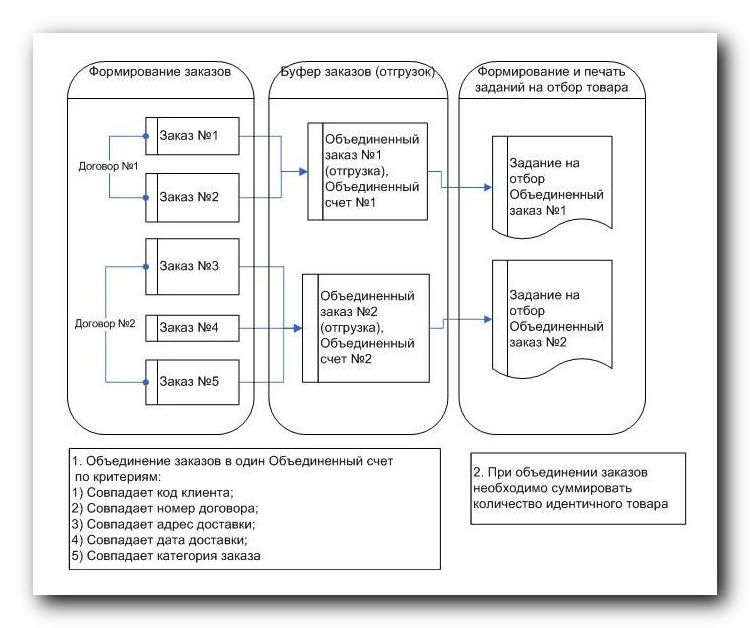
Обмен информацией между информационными системами склада и коммерческого отдела
В таблице 1 отражены основные виды информации, которая используется различными подразделениями предприятия в процессе комплектации заказов клиентов.
Таблица 1.
Вид информации | Источник информации | Потребитель информации |
Количество товара, партии, серии | Для обеспечения достоверности информации о товаре необходимо регистрировать все операции по перемещению товара в АСУ склада, проводить своевременные инвентаризации, особенно в случае выявления недостач и пересортицы в ячейках склада | Менеджер коммерческого отдела своевременно информирует клиента о наличии или отсутствии товара на складеСотрудники склада в ходе работы над претензиями клиентов используют информацию о наличии и движении товаров на складе для подтверждения обоснованности претензии и выявления ответственного за ошибку |
Количество базовых единиц (штук) в транспортной или производственной таре | При приемке товара в АСУ склада вносится информация о видах транспортных единиц | Менеджер коммерческого отдела при приеме заказа ориентирует покупателя на количество товара, кратное упаковке. Таким образом, сокращается необходимость вскрывать короба, целые упаковки, что, в свою очередь, приводит к сокращению времени на комплектацию и ошибок в заказе |
Статус выполнения заказа | На всех этапах прохождения заказа по подразделениям компании сотрудники формируют различные внутренние документы и присваивают им статусы (например, запланирован, в работе, завершен) | Менеджеры по работе с клиентами могут отслеживать состояние заказа, своевременно согласовывать с клиентом время отгрузки или, например, возможные изменения в заказе |
Суммарный объем заказа, количество грузовых мест, габаритные характеристики грузовых мест | Информация заносится в АСУ склада после завершения упаковки заказа | В дальнейшем используется сотрудниками транспортного отдела при планировании маршрутов, рейсов, транспортных средств |
Планирование операции отбора и выдача задания комплектовщикам
Оптимизация операции планирования отбора в основном связана с возможностями современных систем управления складом. Системы автоматизации склада, которые применяет в своей работе AXELOT, обеспечивают выполнение двух блоков функций. Во-первых, информационная система работает как хранилище огромного количества информации о товарах, их сериях, партиях, требуемых условиях хранения, сроках годности, типоразмерах упаковки, уровнях вложений и т.д. Во-вторых, заложенные алгоритмы размещения и отбора могут выполнять управляющую функцию, позволяя оператору склада автоматически формировать задания и распределять их между кладовщиками, грузчиками, водителями высотной техники.
Иногда в процессе выполнения заказов клиентов менеджером по продажам практикуется резервирование определенного товара. Это может привести к увеличению уровня запаса, так как резервируется обычно большее количество товара, чем потом отгружается. Также может возникнуть ситуация возникновения неликвидного товара с истекающими или истекшими сроками годности, поскольку любой менеджер по продажам прежде всего будет стремиться обеспечить своего покупателя лучшим товаром.
Резервирование товаров под заказы клиентов рекомендуется осуществлять автоматически при планировании операции отбора, согласно заложенному в АСУ склада алгоритму. Основополагающим правилом в этом алгоритме является определенный заранее порядок отбора товара на складе по партии или серии:
1. FIFO (first-in, first-out) — «первым входит — первым выходит» — отгружаются товары из партии, поступившей на склад раньше других.
2. LIFO (last-in, first-out) — «последним входит — первым выходит» — большим приоритетом при отгрузке обладает товар из партии, поступившей на склад позже других.
3. FEFO (first-ended, first-out) — «первым заканчивается — первым выходит». Как правило, в качестве критерия, определяющего приоритет отгрузки, используется срок годности: товары с меньшим остаточным сроком годности отгружаются в первую очередь.
4. LEFO (last-ended, first-out) — «последним заканчивается — первым выходит» — товары с наибольшим остаточным сроком годности отгружаются в первую очередь.
Задание складу на отбор товара из мест хранения в заказ поступает с учетом вышеперечисленных правил. Преимущественно при отгрузке клиентам реализуется порядок отбора FIFO (непродовольственная группа товаров) или FEFO (фармацевтика, продукты, другие товары, имеющие ограниченные сроки годности).
Помимо партий и серий при планировании отбора учитываются:
Вид транспортной единицы товара. На складах, где практикуется отгрузка мелкими упаковками и отдельными штуками, как правило, выделяют зону штучного отбора. При этом отгрузка целыми паллетами происходит из резервной (оптовой) области склада.
Область размещения товара на складе. В случае если склад находится в многоэтажном здании или на складе, существует несколько помещений с различными условиями хранения, позиции в заказе целесообразно разделить на несколько заданий отбора в соответствии с существующими областями.
Маршрут комплектовщика. При формировании задания на отбор целесообразно сортировать строки в соответствии с очередностью обхода мест хранения комплектовщиком. Маршруты движения техники и персонала по складу определяются на этапе разработки планировки складского комплекса. В АСУ склада маршрут задается с помощью назначения рейтинга ячеек. Маршруты комплектовщиков строятся согласно приведенным ниже правилам.
Общие правила формирования маршрута комплектовщика:
- Маршрут комплектовщика должен проходить по наикратчайшему пути обхода мест отбора товара и исключать лишние перемещения сотрудника, в том числе, и для использования подручных средств (стремянки, штабелера).
- Желательно организовать движение таким образом, чтобы комплектовщикам не приходилось дважды проходить по одному проходу.
- Начало и окончание маршрута комплектовщиков должны быть также оптимально сориентированы относительно месторасположения зоны экспедиции отгрузки.
- Информационная система управления складом должна позволять строить маршрут комплектовщика вне зависимости от обозначения мест хранения на складе.
- В случае если часть позиций заказа подлежит отбору из всех ярусов зоны отбора, в том числе, и труднодоступных, необходимо отбор с труднодоступных ярусов выделить в отдельное задание. Под труднодоступными ярусами подразумеваются верхние ярусы стеллажей, товар с которых комплектовщик может отобрать только с помощью вспомогательных средств или механизмов. Таким образом, комплектовщик дважды проходит по маршруту, сначала отбирая товары из нижних ярусов, а затем второй раз отбирает товары из верхних ярусов, пользуясь стремянкой или штабелером. Общее время на отбор товара по заказу сокращается.
Передача отобранного заказа в зону контроля. Проверка и упаковка товара
Для того чтобы снизить риск недостачи или пересортицы в заказах клиентов, на складе используют функцию выходного контроля. После завершения отбора заказы передают бригадам контролеров и упаковщиков, которые проверяют соответствие отобранного товара данным в заказе, упаковывают заказы, формируя грузовые места, при необходимости маркируют товар и/или заказы. Как правило, зона проверки и упаковки заказов располагается в непосредственной близости к зоне отгрузки.
Если в ходе проверки отобранного товара контролер выявляет несоответствие с заказанным количеством (недостача, излишки, пересортица), оператору склада следует сформировать задание на инвентаризацию ячеек, в которых размещен товар данного наименования, а затем сформировать задание на размещение излишка на складе и отбор недостающего количества по заказу.
Несмотря на то, что временная блокировка ячеек и проведение инвентаризации может затормозить работу склада, консультанты AXELOT настоятельно рекомендуют осуществлять эти операции. Иначе невозможно обеспечить наличие актуальной и достоверной информации по количеству товаров на складе.
Для быстрого выполнения операции контроля в задании на отбор рекомендуется указывать, к какому столу контроля необходимо переместить отобранный товар.
В случае, когда заказ разбит на несколько заданий, указание номера стола контроля позволит консолидировать все части заказа уже на этом этапе.
Даже если заказ не разделен на несколько частей, отметка о номере стола контроля, к которому необходимо переместить товар, поможет равномерно распределить заказы между контролерами. Для этого в АСУ склада должна накапливаться информация об общем объеме работ, выполненных контролерами за текущую смену.
Скорость контроля подобранных заказов зависит от объема заказа, количества строк в заказе, количества упаковок в заказе, веса заказа. Для анализа объема работ, выполненного контролером, обычно достаточно использовать один параметр — объем заказа.
Основной принцип, заложенный в алгоритм распределения заказов в зоне контроля, следующий: очередной подобранный заказ должен быть помещен на стол контроля с наименьшим суммарным объемом поступивших ранее заказов (рис.3.).
Помимо равномерного распределения нагрузки и консолидации частей заказа, быструю и качественную работу контролера обеспечит оборудованное и хорошо освещенное рабочее место. Важно, чтобы всегда в наличии было достаточное количество упаковочного материала.
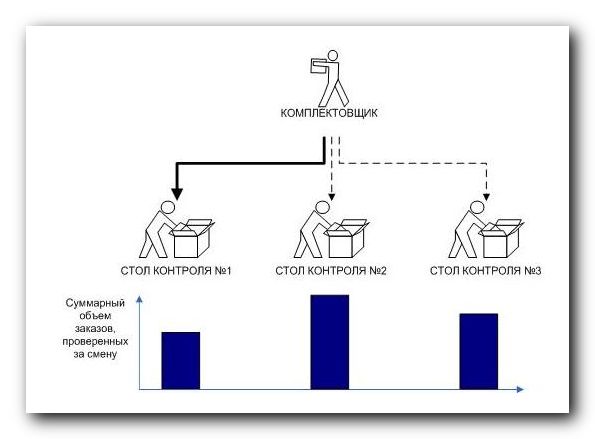
В заключение хотелось бы сказать несколько слов о проблеме соблюдения техники безопасности. К сожалению, посещая склады, нередко можно наблюдать, как сотрудники склада в ходе комплектации заказов поднимаются к верхним ярусам стеллажей, стоя на вилах штабелера, либо взбираются по стеллажу, используя горизонтальные балки как ступеньки лестницы. Это рано или поздно приводит к трагическим последствиям. Поэтому при разработке планировки склада и технологии выполнения складских операций необходимо обеспечить предотвращение таких случаев. Этому будут способствовать следующие меры:
- Выделение активной зоны отбора коробами, упаковками, штуками в нижних ярусах паллетных стеллажей, либо организация отдельной зоны отбора с полочными стеллажами небольшой высоты
- Своевременное пополнение товаром зоны отбора
- Использование верхних труднодоступных ярусов только для хранения товара и отбора товара целыми паллетами с помощью штабелера
- Разделение во времени операций, выполняемых штабелером и выполняемых комплектовщиком вручную, что исключит возможность работы людей и техники в одном проезде
Таким образом, чтобы обеспечить высокую эффективность процесса комплектации заказов, необходим, во-первых, грамотный и тщательный подход к проектированию складских зон и разработке технологических операций, а во-вторых, максимальное использование возможностей современных средств автоматизации.
Функционирование складского комплекса, спроектированного с учетом характеристик товаров и специфики работы предприятия, потребует меньшее количество ресурсов для переработки грузов, при условии сохранения стабильной и безопасной работы персонала склада.
Правильно подобранная система управления складом позволит наладить своевременный обмен точной и полной информацией между подразделениями компании, автоматизировать процесс принятия многих управленческих решений. Но, независимо от того, решаются ли эти задачи силами сотрудников предприятия, либо с привлечением консультантов по технологическому проектированию и автоматизации складов, необходимо учитывать, что именно комплексный подход позволит получить ощутимый результат для предприятия в целом.
Ольга Каверина, консультант по складской логистике AXELOT